Retired Maj. Gen. Kimberly A. Crider moderated a discussion on “Unlocking the Power of Digital Engineering” with retired Brig. Gen. Steve J. Bleymaier of Aerospace and Defense, Ansys; Scott Nowlin of BAE Systems; and Dave Stagney of Pratt & Whitney, Sept. 21, 2022, at AFA’s Air, Space & Cyber Conference. Watch the video or read the transcript below. This transcript is made possible by the sponsorship of JobsOhio.
If your firewall blocks YouTube, try this link instead.
Maj. Gen. Kimberly A. Crider (Ret.):
I hope everybody’s doing well this morning, day three of this amazing conference. Well welcome to the Unlocking the Power of Digital Engineering panel. I was just saying to General Richardson, thank you for joining us this morning, sir. This is going to be an enthralling dialogue on this topic, and I know we’ve got a lot of folks out there that are doing some amazing things in the digital engineering space. And our panelists here are going to talk to you about some really cool things that are happening in their world that I think we can all take advantage of. So I’m Kim Crider and it’s my pleasure to be your panel host today. As I said, I see lots of familiar faces out there, so thank you, friends, for being here for what I am sure is going to be a rich panel discussion.
As many of you know, I retired last year in June and prior to my retirement, I was the Chief Technology Innovation Officer for the United States Space Force. These days, I’m involved in a number of exciting projects with a variety of organizations, including Catalyst Campus for Technology and Innovation, I see Robin out there, as well as my role as the Executive Chair for AI Innovation for National Security and Defense at Deloitte, where we’re advancing digital engineering and immersive simulation capabilities to optimize the design, development, production, manufacturing, launch, operation and sustainment of national security and civil space capabilities. So let me take a moment and let each of our panel members introduce themselves to you. We’ll start with you, Steve.
Brig. Gen. Steve J. Bleymaier (Ret.):
Thank you, General Crider. So I’m Steve Bleymaier. I retired from the Air Force three years ago and joined Ansys two and a half years ago. And Ansys is an engineering simulation company. And I am not an engineer, so I think I’m here to be the translator for all the non-engineers that are in the audience. I was in the sustainment side of the Air Force. So I want to start with why? So in two minutes, basically digital engineering is about accelerating acquisition and going faster and decreasing lifecycle costs. In 2018, the NDS said that we need to move towards becoming a more lethal force. I haven’t read the 2022 NDS yet because it’s classified. But to increase lethality, you must accelerate acquisition, you must reduce costs, you must reduce risk and you must increase readiness, reliability and availability. In May of last year, SAF/AQ sent out a memo saying digital acquisition holds the key to unleashing the speed and agility we need to field capability at the tempo required to win a future conflict with a pure competitor.
Our pure competitor, China, increased its military budget 900% between 1990 and 2017 and they have 2030 goals for AI and ML, and to be the dominant power. And they are nationally mobilized and they are moving out towards achieving their goals and objectives. And they don’t have the barriers that we have. So that should give us a sense of urgency. The burning platform is China. Just ask [inaudible 00:03:34]. But even knowing that, knowing about China, there still seems to not be the sense of urgency there should be with accelerating and adopting digital engineering. Christian Brose, the author, says that the only way to deter war is to clearly be capable of winning a war. Two years ago, he wrote The Kill Chain and in The Kill Chain, you basically want to gain a better understanding so that you can make better decisions and produce better actions to achieve objectives. But as one war fighter said, none of my things can talk to each other, hence the need for JADC2.
And Christian Brose said that the root cause of the problem that the things couldn’t talk to each other was that available technology was not available to the military, or is not available to the military. So in business, we have to change or become obsolete. And the classic example is Netflix. General Brown says accelerate change or lose and Christian Brose said that we have to reimagine the ends, ways and means of war. General Richardson yesterday said that he’s focused on the ways and changing those ways. Well digital engineering technology is available today, but it’s not necessarily available to the military writ large. Now, there’s silos that are mainly the classified where they have it, but not the masses. So I like to say not only do we need to unlock digital engineering, but we need to unleash it. We need to unlock it and get it into the hands of the military. And then once you have it, you need to unleash it like that husky that wants off the leash.
Otherwise, you’re not going to experience the power and the full value and its ability to accelerate acquisition across the lifecycle. So with thinking about China again, it’s time for us to move out. And as we like to say in the engineering simulation world, take a leap of certainty. I know that was longer than two minutes.
Maj. Gen. Kimberly A. Crider (Ret.):
That’s okay. No, you’ve put it out there, Steve. Thank you so much. Go ahead, Scott.
Dr. Scott Nowlin:
Yeah. Hi, I’m Scotty Nowlin from BAE Systems, retired five years ago after a career as a developmental engineer doing flight test engineering, some time teaching at the academy, some time doing systems engineering, mechanical engineering. Digital engineering is a reality today. It’ll ought to be a reality for all of you no matter what your function is, right? Financial functions, operation support, maintenance, you all deserve to benefit from systems engineering or from digital engineering and systems engineering. We’ve been doing it for five years, so I’m blessed to be working with about 800 people at Hill Air Force base on the ICBM integration support contract.
We’re a prime on that with a number of great subcontractors. We’re partnered with great companies like Ansys to bring modeling and architecture and linking it from original requirements, linking it along a digital thread, I hope you don’t get bored by all the buzzwords today, linking it along a digital thread, two modeling and simulation tools, two supply chain and sustainment issues. And we’ll get into more of that with some of the Q@A we’re going to be involved in. So I want to thank the AFA for being here and thank all the service members who are here and all those who support the military. Thanks for this opportunity.
Maj. Gen. Kimberly A. Crider (Ret.):
Thank you, Scott. Amanda.
Amanda Brown:
Hi, my name is Amanda Brown. I’m the Director of Digital Transformation for a Sixth-Gen Fighter program at Pratt & Whitney. My role covers the digital and agile transformation that all of our military development programs need to make in order to successfully deliver our customers’ requirements. I have a bachelor’s in mechanical engineering, so don’t hold it against us. I have a PE license, an MBA and 25 years at Pratt & Whitney. So I’m coming from a position of… Well if you were to examine my career, you would find a very processed slant to everything that I’ve done. I’ve been a mechanical design engineer on parts, module integration, working at the system level with our class one engineering, change process, configuration management, things like that.
But every role I’ve had, I’ve been inordinately bothered by inefficiency. And heaven forbid, you ask me to type the same information into two fields, I just get irate because I find it so annoying. So it has made me particularly responsive to this current role. I’ve spent the last five years working in model-based and digital transformation areas and I am so excited to see our industry, our customers, our competitors, all responding to this need to change not only what we do, but how we do it. Not only the products that we make, but the processes we use to make those products. So I am very pleased to be here today and I look forward to our chat.
Maj. Gen. Kimberly A. Crider (Ret.):
Wonderful. Well thank you so much. Steve, you really laid it out there. We’ve got to unlock it and we got to unleash it. So we’re going to get into that right away. I think this panel is ready to just get after it. And I want to start with Scott. We’re going to start with you in the middle there, Scott. So you guys, each of you, I think have some really great stories that you can share about where digital engineering is successful and how it’s working in your organizations in industry and in the government. And Scott, as you mentioned, the role that you’re playing at BAE right now is directly contributing to some of our programs there at Ogden. So help us understand, Scott, from a DOD perspective, where is digital engineering really happening? And what results are you seeing that are being delivered by applying digital engineering?
Dr. Scott Nowlin:
So first some terminology. I would encourage everybody to dig out the 2018 digital engineering strategy for a good summary of what the heck we’re talking about when we use that buzzword digital engineering, I appreciate General Richardson coming up with some more specific terminology like digital material management. We’re living digital acquisition with the Sentinel program, previously the GBSD program. I’ve got lots of specific scar tissue with watching that program mature from milestone A to milestone B. And now, we’re living the dream with digital sustainment with Minuteman 3, a 50-year-old weapon system that is going digital where and when it makes sense. So my first hand knowledge is with this breadth of experience along the lifecycle, right? So the left hand side there, we’re dealing with turning paper requirements into government reference architectures that are then put on contract with primes, all the way down to our right side where bills of materials are driven by PLMs, product lifecycle management tools.
I know it’s happening in other places, I see it. I come to venues like this and I see it with industry booths and I hear about it from the stage from senior leaders. And so without knowing all those specifics, I would just encourage folks read that strategy, see where you’re already using those digital capabilities and then look for ways to integrate because the real power of this nebulous thing called digital engineering and the digital tools that you’re using and the digital data that you’re accessing from your seat as a financial analyst, from your seat as an operational planner, from your seat as a maintenance troop out on the flight line is to link that with the other data that’s out there. So I won’t try to give a whole lot of other examples. I know that Pratt & Whitney’s all in though with digital models of very complex systems like air breathing turbine engines. So lots of examples out there and I would just encourage everybody to look for those in your own workplace and integrate with them.
Maj. Gen. Kimberly A. Crider (Ret.):
Thank you. All right, well let’s hear about some of those examples on the industry sides. Scott laid out some things that are happening in the Sentinel program and the ways in which we’re implementing these capabilities for success. But industry’s been ahead of this for some time and I know Pratt & Whitney’s been doing some really great things. So Amanda, help us understand how has digital engineering been applied in industry? What results have you seen?
Amanda Brown:
Yeah, thank you. And just building off of what Scott was describing, we are seeing applications and successes in every corner of the business. We call it digital engineering, but it involves and it impacts every corner of our business. So some of the recent examples, we had a couple, we had two digital PDRs, preliminary design reviews over the summer. And these were examples where a typically very burdensome labor intensive process of lots of PowerPoint slides being sent back and forth and being very static and difficult to digest, difficult to prepare and really difficult to store for later data mining was replaced by using system modeling. Our model-based systems engineering capabilities and organization have really grown through these demonstrated examples over just the past year where document-based processes and information is replaced by model-based, or models that represent the same information and convey the data in reusable and structured forms. So now, requirements don’t come from a customer as a 500-page sentence document. It is a system model that we can then decompose, distribute across our organizations and then measure actuals against. So everything comes as data, is treated as data and gets used as data.
In the two examples I was talking about this summer, we saw what was estimated to be a 48-month process based on our legacy ways of doing things get improved by about a 20-month improvement. So we cut it almost in half by using these digital and model-based ways of communicating and of sharing information. One of the programs in particular found again a very burdensome process that had to do with our control schedule generation for fuel burn. It was normally a many months process was executed in several days and we were elated by this. And then the question is what do you do with that unlock? So now, you’ve unlocked some great capacity and the beauty of digital is it gives you choices. So either you’re three months ahead of schedule, which is amazing and valuable from our customer’s perspective if you are meeting the requirement. But if you’re three months ahead of schedule and you’re read for your requirement, that doesn’t do you much good except that now you have plenty of time to add additional iterations, perform more requirements evaluation. And so you can either translate that unlock into better performance or schedule improvement.
And there are other examples where you get choices than in a digital world that simply aren’t available when you’re doing everything paper-based.
Maj. Gen. Kimberly A. Crider (Ret.):
That’s great. Wow. So really seeing some value added results coming from the application of digital, saving time, saving money, capturing that unlock and turning it into value for the customers. But we know it’s hard. Steve, you gave us the sense of there’s this burning platform out there. We know China is the pacing threat and we’ve got to get after it. But it’s hard. It’s hard. So in your experience, why is it so hard for organizations to adopt? And what are some of the impediments, what can we do about that?
Brig. Gen. Steve J. Bleymaier (Ret.):
So that’s an excellent topic and I’ll cover it focusing on the organization being the Air Force and the Space Force. Although there’s many similarities to what I’m going to say to industry, but the context are completely different in many ways. So we can look at this through the lenses of technology, process, culture and training and funding. It’s not a technology problem. The technology is available and it’s open architecture. But sometimes, technology runs into culture in cots versus gots and that’s just a reality. And then anything that is a change like digital engineering or is new, a new process, it takes time to get up to speed. So look at the process, the current processes, they are outdated. And one of General Richardson’s lines of effort is to revolutionize processes and that’s excellent. They need to do that to allow the Airmen and the Guardians to adopt digital tools. Just look at airworthiness and how we do it or how it’s done in the military. It’s still based on a paper method. While commercial industry is doing like [inaudible 00:17:30] certification using models for the past 20 years.
Test processes are focused around physical testing, but the physical infrastructure of test and evaluation, it’s expensive to fix and there’s huge backlogs. So are they at a fork in the road? Do they invest more and commit to computing power and software to do more virtual tests? Sustainment, the sustainment arena is very challenging. There’s often no drawings, there’s no digital thread, there’s no requirements for things like condition-based maintenance and there’s no dedicated funding. And data analytics and artificial intelligence, that’s currently the process that has been chosen and that’s slow. But data analytics and physics-based models, they’re not in competition. In fact, you can actually fuse them together. You can take data analytics and artificial intelligence and sustainment and you confuse it with physics-based models to create a hybrid digital tune and get a higher accuracy rate. So culture, culture and training. You all have heard the saying that culture eats strategy for breakfast, right? So culture, it often keeps people from being able to hit the, “I believe,” button,
Digital engineering and model simulation analysis and taking the place of build and test and physically test, that’s a big change. So that’s difficult to make happen. And it’s hard for folks to hit the, “I believe,” button. So couple that with the fact that in Lifecycle Management Center for example, 35% of the engineers are retirement eligible, there’s a thousand vacancies, the SPOs are manned at about 50% of engineers. So they are stretched thin. So when you introduce this type of a process change, it’s difficult in that context. So for the culture, really the DAF needs to transform its people because digital engineering is not about hiring people to do digital engineering, you’re going to use the same people, but you’re going to transform the processes. So you’ve got to train them to do that. So training and building the digital workforce means providing them the tools that are available. And culture change of course requires leadership at all levels. And then finally, funding. The best vision in the world is just a good idea until you fund it.
Yesterday, the honorable Hunter said that one of his priorities is to transform the acquisition system into the 21st century, moving to a software-based acquisition system, changing business arrangements and processes, adding digital thread and increasing acquisition speed. And that is awesome. But nothing in the DOD is a priority until it’s funded. So this is an enterprise problem, that’s how I see it. And really to achieve the full benefit and the value of digital engineering, it requires an enterprise ecosystem. But it’s currently funded at the SPO level, so it has to compete with SPO resources. So what you’ll end up is siloed capabilities that aren’t connected and there at different levels of maturity and scale. So that’s a mismatch.
Maj. Gen. Kimberly A. Crider (Ret.):
Wow. So there’s a lot there, right? There’s process challenges. We’ve got to do the hard work of revolutionizing these processes. There’s limited data available. Of course, we know the data that is available is typically not clean or curated very well quality. So there’s time that’s needed to deal with that. You talked about the culture in and of itself of just adapting to a new way of working and operating. There’s that resistance that goes along with limited skills or needing to develop and up the skill level of our staff. And of course, funding. That’s a major constraint. So you’ve laid out some really high level enterprise challenges that are for sure creating some impediments. But yet on the ground, certainly again we’ve seen with programs like Sentinel, GBSD that we’ve gotten through some of that. Scott, tell us what’s going on there. How have you begun to overcome some of these barriers to adoption that are real? And I’m sure many in the audience are feeling these challenges today.
Dr. Scott Nowlin:
So Steve did a great job hitting on some of the major touchpoints across what I think of as being the quad chart of digital engineering, right? I think about the people and the processes and the tools and the infrastructure. Sentinel, GBSD was fortunate to have the resources to invest in infrastructure. I’m not going to talk a lot about that, especially because of the classification level they have to act at. The processes. Steve did a great job talking about that. Tools, there are many, many different tools out there. Let me go back to the people because this room is full of people and you all ought to be thinking about on my next civilian appraisal, on my next EPR, OPR, on my next CPARs that I’m going to give to my support contractor or my prime, where’s the word digital going to appear? What impact am I having on the organization because I’m willing to step out and get innovative?
So if I think about the people at your level, wherever you are in the organization from a four star all the way down to… There’s probably some Arnold Air Society members in here, right, who are doing capstone projects in college. Where are you looking to apply digital from your seat? I know within BAE Systems, we’re implementing culture change at a boots on the ground level. We do MBSE boot camps where we bring our employees in for a week long program where we get into a CSML model. And yes, they can go take a class and learn about CSML and prepare for CSML 2.0 as a modeling language, but they don’t see it in action until they can trace. And one of the benefits we’ve seen is an engineer being able to sit down in front of an architecture of Minuteman 3 that captures 1,400 configuration items and be able to identify the departing baseline for a change.
In other words, you want to take out the guidance computer, the Minuteman 3 as a notional example. Instead of spending days looking through drawings and chasing down interface control documents, in minutes you can generate a report that shows if I rip the brain out of the Minuteman 3 in its guidance computer, how that ripples across the weapon system and what other piece parts does it touch down to a chip level if you want to go that deep, if you’ve decided to model that deep. So really the people issue as it percolates up, the return on investments come when you’re able to invest in your people I would say first and foremost. And that includes leadership getting smart on where to make the investments because you can’t boil the ocean. Minuteman 3 for example cannot afford to become a digital weapon system. They don’t have the time or the resources. But Sentinel was born digital starting from a government reference architecture that captured its requirements in a digital framework and they’re now able to reap those benefits.
Maj. Gen. Kimberly A. Crider (Ret.):
All right. So invest in your people first, build digital engineering from there. Leadership has a critical role in that. And hold ourselves accountable are some of the things that I heard there. Where are you going to find digital in your personal performance outcomes that you’re going to hold yourself accountable for? I’m sure it wasn’t easy for Pratt & Whitney to get started either. You’re a big industrial age company as well and while you guys have achieved some significant successes and have done some things that have really started to lead the way, how did you get traction in this? Tell us, Amanda, how that got started and what are some of the successes that led to you being able to move out?
Amanda Brown:
Yeah. I think Steve, you hit the nail on the head. Culture change is at the heart of digital transformation, agile transformation, all of it. I think the best way to engender more success is to show success. So we started, as you might expect, with some small pilots, some energized excited people who just wanted to go and explore this. They became knowledgeable and then they pushed it with their management and then were able to grow a critical mass of energy behind it. So our model-based systems engineering and model-based product definition are the two areas that are probably the farthest ahead. And if you’ve worked with model-based product definition, this is eliminating 2D drawings and replacing it with 3D forms of product definition where all of the engineering data that’s typically text only, dumb text on a drawing is embedded as machine readable content in the 3D solid model. So now, you have reusable data. So our model-based product definition team did a couple of pilots and had some great success and we demonstrated how you can create this 3D form of product definition that’s easy to access.
You don’t need a specialty CAD license or fancy CAD training, you can use some light CAD readers that are on the market. And then we demonstrated how our supply base, a producer outside of Pratt & Whitney, can consume, that’s file import, right? Not typing the information over again, but can consume the 3D product definition, the digital data and use it to build their CNC program, their CMM program, their op sheets, and then perform the inspection in 3D ways. And they actually did it. And those early successes have to happen for culture change to ever occur. Not only do we need to provide training like Scott was mentioning, there are some new things that people need training on that you can’t just thrust them into an unknown environment. But it’s critical that the senior leadership be brought along the journey and be prepared for things that are different. Just being able to show a little bit of vulnerability is something that’s foreign at Pratt & Whitney and probably in most of the industry environments.
And to go in there and say, “I don’t know if this is going to work, but I think it has a lot of potential and we need to try this.” Creating leaders who are willing to respond to that, provide top cover for these energetic teams. It is an innovation and an exploration. We don’t know the crystal clear path to get there and I think the advocacy from leadership to allow the space for innovation has been a key point in our success. It’s also been critical for us that we go the full enterprise and the full lifecycle. And Pratt & Whitney Engineering is one major organization within our company and there are other major organizations just as big and just as loud and just as opinionated. And if you do digital engineering and engineering alone, you’ll never be successful. You just won’t get there. So bringing the operations community, the human resources community, the finance community, all these other parts of our organization along because they are impacted, You can’t run a good engineering project if you don’t have financial data on your actuals.
Are my people charging? Are they spending? Am I behind? Am I ahead? All the EVMS stuff, hey that’s data. I need that data to be reusable and accessible. So I think a lot of our success has been because we are forcing, and it’s not always easy, the conversation to occur across the enterprise and across the lifecycle. So by lifecycle, I mean we tend to have different communities of people who work early conceptual design, different communities of people who work are production support and design, different communities of people who support the aftermarket. Again, we want that data leveraged up and down the lifecycle. If you have actual manufacturing data, we want to use it to evaluate our service part. Can it go back in for another thousand cycles? Because we know that the part was on the high side of the tolerance band or no, it was on the low side of the tolerance band, we better pull it and replace it now. These are decisions that Usage Based Lifing lets us make.
This is something we’ve been instituting on the F119 fleet where we take actual manufacturing and actual flight history data to determine additional life or usability of parts rather than just using nominals or typical flight conditions. And having that data accessible unlocks a lot of doors that can not only extend life on wing, but can then let us step change, improve the performance of a given aircraft or engine based on using that data in different ways.
Maj. Gen. Kimberly A. Crider (Ret.):
Wow. So not only is leadership critical and pulled on that thread for us a little bit, which was great to see that how important that’s been in your organization in getting those early wins as successes with the pilots, having leaders be willing to allow for failure and experimentation. But you’ve also reinforced the point that was made earlier about the criticality of data and making that data available across the full lifecycle so you can really start to reap the benefits from design all the way through to sustainment and be able to unlock those silos that we all operate in and find insights all along that lifecycle.
I want to jump ahead a little bit here to some terminology. And you guys have talked on some of this a little bit, but I want to make sure that we level set everybody on some of this. What Amanda was just talking about in terms of leveraging data across the lifecycle speaks to what we typically refer to as the digital thread. And I want to ask Steve to help us understand what is it we mean by a digital thread? I know his company works a lot in helping organizations put in place the types of tools and capabilities that will enable the digital thread and also be able to empower a digital twin. So tell us, Steve, a little bit about what is a digital thread? What’s a digital twin? How does it fit into this whole activity of digital engineering that we’re trying to get our arms around?
Brig. Gen. Steve J. Bleymaier (Ret.):
Sure, and I’ll try to be fast. So digital twin, it’s not just doing simulation, it’s not just building a CAD model, digital twin is about connecting a physical system and a digital model in real time or near real time so that you can do prognostics and other activities across the lifecycle. This could be taking telemetry data off of a satellite and then moving it offline to do anomaly resolution before putting it back into and physically implementing it on the space asset. Digital twins can be multi-fidelity. They don’t all have to have physics and be physics-based models. They could just contain data analytics and AI, or you can combine the two and it really depends on the criticality of the system or the component that you are producing the digital twin for. Just like Scotty mentioned earlier, we wouldn’t have the funds to ever be able to do digital twin on all of our fielded systems and every component on those systems. So you can be surgical and you can produce the right digital twin that you need.
And if you just used data analytics and artificial intelligence, you get to about an 80% level of accuracy, like I mentioned earlier. When you combine those together with physics, you can get up to 98% level of accuracy. The twin can also be used for activities across the lifecycle. So these include things like virtual verification of performance, operational decision making in wartime training, predictive maintenance on the asset, and even developing a future system to include training and validation of AI and ML capabilities as those come on board more and more. And then digital trend, this is commonly thought of as the digital fabric that connects the different parts of the lifecycle together. And that digital thread allows a model to progress in fidelity from research and development to acquisition, to test, to deployment, to operations and to sustainment.
And as it goes along that path, you’re aggregating that data. And so then when you field it and it performs, that data can get fed back into the digital twin. And then you can compare it against what was expected and what was required. And you’ll have that traceability and that repeatability all the way back to the as designed, to the as manufactured and to the as fielded versions. And you’ll be able to see what has changed and figure out the root cause of why it’s changed. And as was I think mentioned earlier, you can accelerate when you have to make a change or an upgrade. You now have that knowledge and that data that was used and produced all the way back in concept development and design. You don’t have to recreate it, which is what has been happening for years and that’s why upgrades take so long.
Maj. Gen. Kimberly A. Crider (Ret.):
Thank you. Well unfortunately, we’re out of time. I’ll tell you, we could go on all afternoon I think talking about this topic of digital engineering and so many great examples here. Thank you for sharing your insights, your success stories, telling us about the challenges and reinforcing the important points of investing in people, investing in data, investing in process, and most of all, just getting started. Just getting started. Unlock it, unleash it, see where it takes you, take advantage of those opportunities to accelerate your capabilities. We have to do this. Thank you for being a part of our panel today. Thank you all for participating. We look forward to chatting with you afterwards.
Dr. Scott Nowlin:
Thanks, everyone.
Amanda Brown:
Thank you.
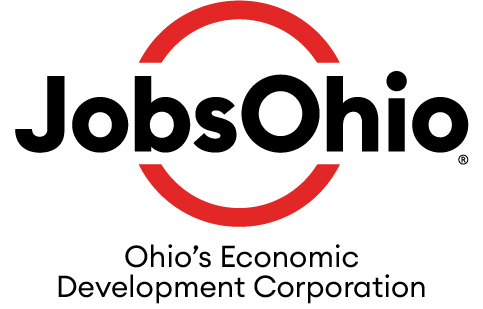