The Air Force Life Cycle Management Center has no set date in mind for retiring the B-1 Lancer, but it does has a multi-pronged approach for keeping the famed bomber credible until the B-21 comes online, focused on:
- Parts obsolescence
- Wear and tear
- Capability for new weapons
Brig. Gen. William Rogers, program executive officer for bombers at AFLCMC, told reporters at the Life Cycle Industry Days conference July 31 the Air Force has dropped its 2018 bomber plan that called for the B-1 and B-2 to retire in the early 2030s, and instead will keep those aircraft viable until the stealthy B-21 is ready to replace them.
The new plan is called a “Bomber Capability Roadmap” and directs investment to combating “obsolescence and diminishing manufacturing sources, which is a key concern of ours on those aging platforms,” Rogers said.
“It’s a common problem across the entire Air Force fleet as aircraft get older,” he noted.
For the B-1 in particular, Rogers said his focus is on making sure the fleet remains capable of sustaining operations and giving military and civilian leaders options, allowing the swing-wing jets to “retire gracefully.”
“How do we ensure the structural aspects of the aircraft … and then, also, what are those key capabilities?” Rogers asked.
One such capability may be using the B-1 as a platform for testing hypersonic weapons. Boeing has offered the Air Force a modular pylon system that could enable the B-1 to do just that, potentially reducing the test load on the B-52, which is entering an intense period of testing new radars, communications, navigation, and engines.
“At this point, we’re really working to first prove the engineering and development work to see if it’s really a viable capability for the B-1,” Rogers said. “We’ve been working with Boeing, [which] has an [independent research and development] pylon that we call the Load Adaptable Modular (LAM) pylon.”
Joe Stupic, head of the B-1 division under Rogers, said the service has conducted ground testing on the pylon, which snaps munitions in like “Lego.”
“If you look at the bottom of the B-1, It’s got a nice round bottom,” Stupic said. “But trying to stick a conformal pylon on it is very hard to do. So what Boeing did was created basically something that could be adapted to any station on the plane with the kit that comes with it. So it’s adaptable, to whichever station you want to mount it to. So that’s the beauty of it.”
Rogers said the program has been successful so far in that a variety of weapons have been successfully mated to the pylon. Stupic said ground tests have studied vibration testing, loads, and “box drops of some JDAMs” as well as with large and heavy shapes.
A flight test carrying “something big” like an inert AGM-183 Air-launched Rapid Response Weapon (ARRW) will be tested in the “September-October timeframe,” Stupic added.
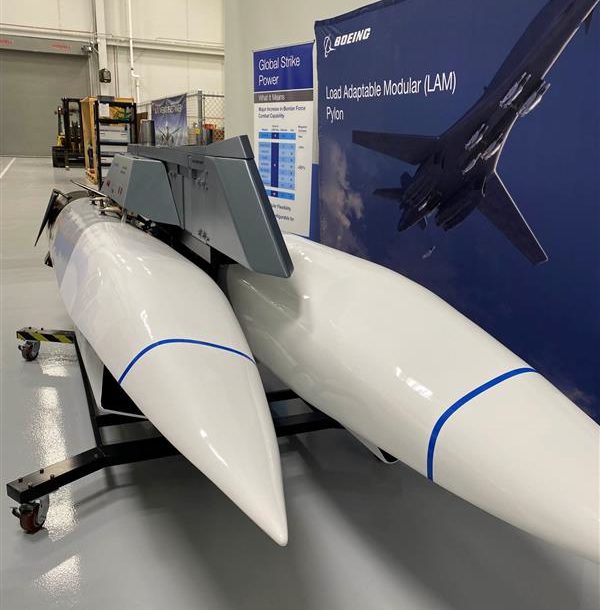
Stupic also said AFLCMC is working around measures that were taken to render the B-1’s external hardpoints inoperative under the START treaty, so they couldn’t carry AGM-86B Air-Launched Cruise Missiles externally.
He said there’s “still the structure where you can mount a pylon and that’s we’re doing the work around to get these pylons hanging, but there’s no more wiring, no more power, no more cruise missile control box. It was all ripped out for the START Treaty. So, a lot of work to wake it up again.”
At the moment, the Air Force is focused on using the LAM pylon for testing weapons, Rogers said. He demurred, however, when asked if it could have other uses.
”Ultimately, we’ll see where the Air Force wants to go; if they see the value or not from an operational perspective,” he noted.
Stress Test
Full-scale structural fatigue testing on a B-1 fuselage carcass and wing is also underway at Boeing’s Tukwila, Wash., facility in order to get ahead of the fleet and see if there are “potential risk areas,” Rogers said. That step that was skipped in the 1980s in the urgency to field the B-1.
Rogers could not quote how many hours the static articles have on them, but the testing has been successful, with nothing to suggest “we’ve got a hard, hard wall ahead of us that we’ve got to work around,” he said.
“Now we’re in the phase where we’re probably going to shut down for approximately the next year and really go through both the fuselage and the wing from an inspection standpoint, and documenting, looking for any of those safety problems or issues,” Rogers said.
At the moment, stress testing on the B-1 wing has progressed to the point where it has more wear and tear than the rest of the fleet, Rogers said. But still more has to be done for officials to get a better sense of the wings’ likely service life—likely another three or four years of testing.
The fuselage is further behind and will likely need five or six more years of stress tests, Rogers added.
“We’re keeping the fleet safe until the B-21 shows up,” Rogers said. “… We can keep that plane flying. It is just hard work.”
Structural issues found by the stress test—cracks, separations, etc.—are being addressed on a secondary structures repair line at the B-1 depot at Tinker Air Force Base, Okla., Rogers said, which keeps more of the remaining B-1s in service and shortens depot time.
Digital Twin
The Air Force also has two B-1 carcasses that have been disassembled at the National Institute of Aviation Research at Wichita State University, Kan., for the purposes of creating digital twins.
“Pretty much all the structural parts” have been scanned twice, Stupic said, to create computer-aided design/digital twins of the B-1 that can help predict structural issues and create a baseline for upgrades.
So far, 4,000 of a planned 51,000 CAD models of the B-1’s structure have been completed, he said.
“And what my engineers intend to do is use those better CAD models for real aircraft, [and] bounce them against the drawings from the 1980s that may or may not have ever been updated,” he noted.
Drawings were rushed for production in the 1980s, he said, and “now I have a model that is good for re-procurement of part ‘X,’” that can be provided to the Defense Logistics Agency, which can then use them for parts competitions.
“Anyone can bid on the darn part because it is not something you need” to reverse-engineer 1980s drawings to build, Stupic explained. Modern processes can rapidly reproduce the needed parts and “we are hoping that will reduce our cycle times,” he said.
While the second digital twin, which looks at large structures, is not expected to yield the same level of structural fidelity models as the real-world stress test at Tukwila, “if the results from [the stress test] starts matching, maybe we don’t have to flutter that wing at Tukwila, maybe I have enough correlating data in the digital model that it’s good enough to use in scenarios like this,” Stupic said.
He added that “everything is cycle time, now. My pitch to my folks is, ‘cycle time in weapons integration and cycle time in software releases.” The B-1 is about to have its first agile software release this fall, he added. “Cycle time is a competitive advantage in this environment.”