TYNDALL AIR FORCE BASE, Fla.—Three new hangars under construction at Tyndall Air Force Base, Fla. could make maintaining the F-35 more efficient than ever, with built-in maintenance facilities, a walkable campus, enhanced wireless connectivity, and other amenities.
“This is a dream for any maintainer,” said Col. Robert Kongaika, commander of the 325th Maintenance Group that will oversee upkeep for the 78 F-35s to be assigned to Tyndall’s 325th Fighter Wing.
The base as a whole is undergoing a $5 billion reconstruction effort after the devastation of Hurricane Michael in 2018. Officials want to make Tyndall the Air Force’s ‘Installation of the Future,’ the model of what the service could look like in years to come—complete with facilities that can withstand the most extreme weather and new technologies to make maintenance and base security faster and better.
But the biggest single investment is going toward Tyndall’s transition from training F-22 students to flying operational F-35s. The three hangars being built, one for each future squadron, are part of what leaders are calling ‘Zone One,’ an area devoted to flightline activities.
The zone includes a maintenance complex, group headquarters, aircraft parking aprons, aircraft support equipment storage, a corrosion control facility, and an F-35A flight simulator building. It is the single largest military construction contract on record in the Air Force database, which dates back to 2008, according to an Air Force release. The construction contract is $532 million, but contingencies and contract oversight brings the total investment to $604 million.
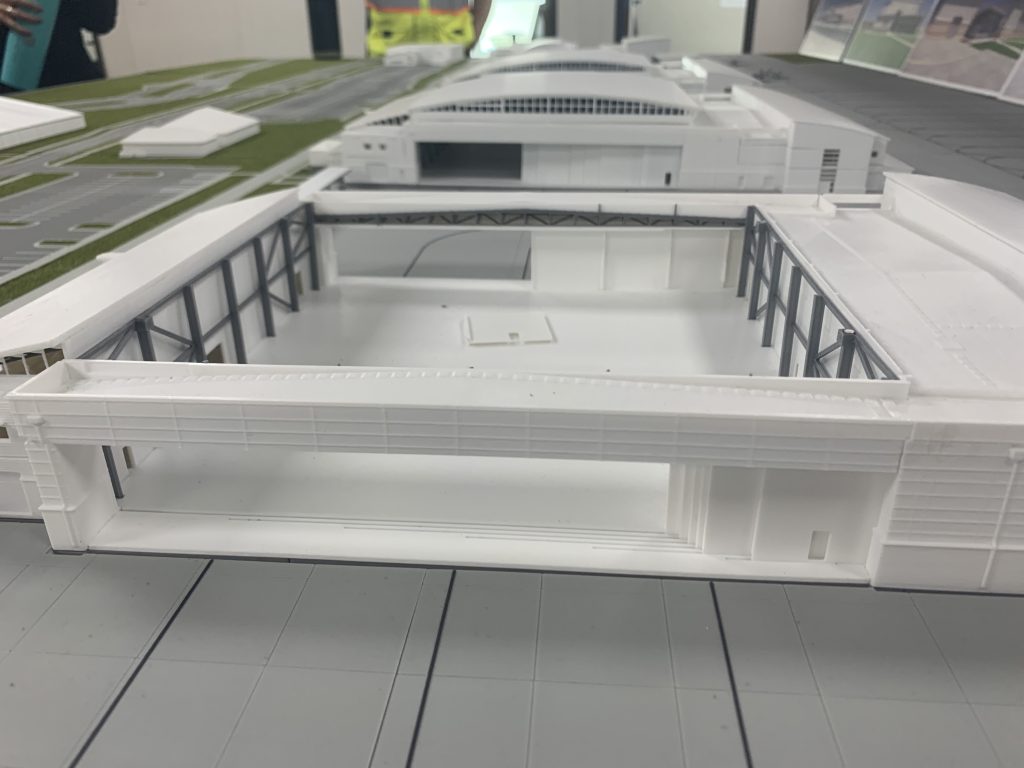
Next Generation Hangars
Officials say that top-dollar price will bring top-of-the-line quality; each hangar will serve as home for both maintainers and pilots for each of the three F-35 squadrons, which should allow for easy cross-pollination, Kongaika said. Hangar doors at either end of the facilities will let jets flow in and out more easily, he said.
Maintenance demands ample electricity to power the aircraft; air for inflating tires or environmental control systems; and water for spraying down the jets. In older hangars, maintainers would bring in noisy aerospace ground equipment that guzzled fuel and generated exhaust, but at Tyndall those utilities will come straight out of the building itself. Kongaika worked with a similar set-up at Luke Air Force Base, Ariz., another F-35 location, where utilities rose up from the hangar floor on hydraulics.
“That’s state-of-the-art, in my opinion, because you’re reducing your thrash: the wasted time it takes to bring in other equipment and take it out,” he said.
Air conditioning and high-speed wireless internet will be built-in rather than bolted on, as is the case in some other facilities. Reliable Wi-Fi is increasingly important to connect tablets and other devices maintainers rely on to fix F-35s. Kongaika envisioned future wrench-turners using augmented reality-equipped headsets or glasses to further streamline the maintenance process.
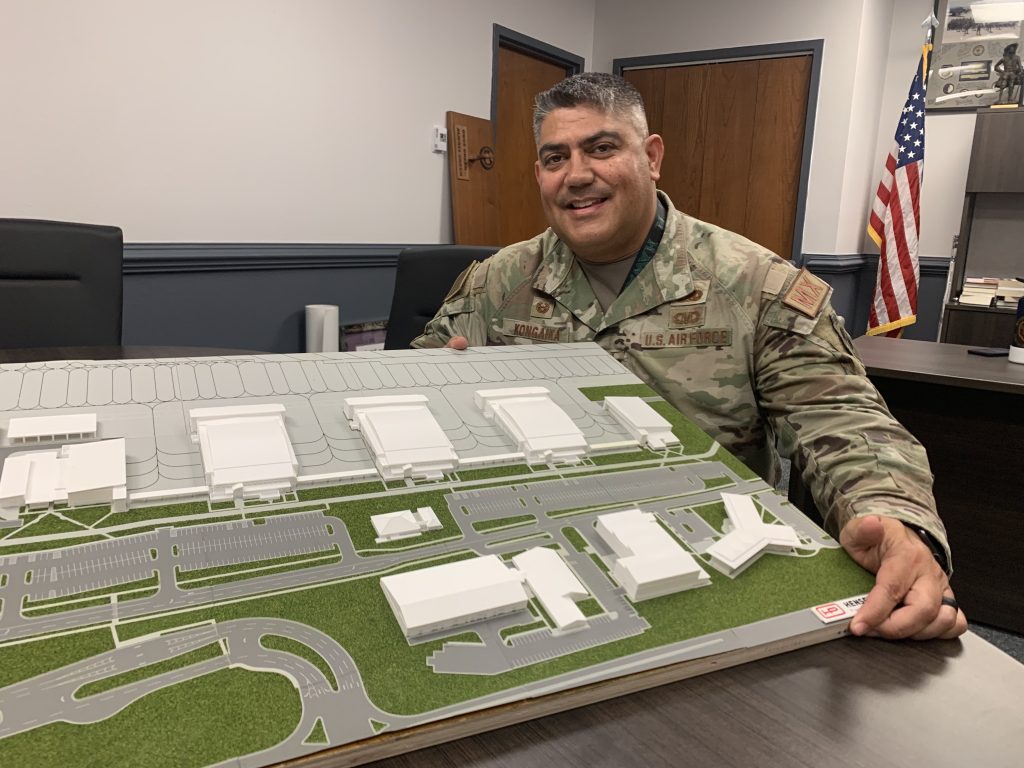
Current Challenges
While Kongaika and other Air Force leaders envision a high-tech future for maintainers, there is an obvious challenge—the hangars will not be completed until 2026, but F-35s with the 95th Fighter Squadron have already begun arriving. The first four landed at Tyndall in early August, with 12 more scheduled by the end of summer 2024. For now, maintainers with the 95th Fighter Generation Squadron work out of a refurbished office space, but the jets remain outside without the benefit of sunshades.
“We’ve got ice machines, we’ve got Gatorade to try and make that as tolerable as possible, but they will be straight up on the open ramp in the Florida sun,” said Maj. Benjamin Flores, commander of the 95th FGS. “That will be something we’ll have to keep a focus on and try to make it as easy as possible for them.”
Another challenge is the scale of the rebuilding effort, where up to 4,000 construction workers rub elbows with operational Airmen. The tight quarters require careful coordination between the 325th Fighter Wing, the Air Force’s Natural Disaster Recovery Division, the U.S. Army Corps of Engineers, and the contractors the corps manages.
“We spend a lot of time trying to look forward to identify where those conflicts could occur and mitigate them before they become an issue,” said Col. Robert Bartlow Jr., chief of the Air Force Civil Engineer Center Natural Disaster Recovery Division. “But things happen all the time where we realize we’ve got a problem and we need to address it.”
For example, one of the tenant units at Tyndall is the 601st Air and Space Operations Center, which plans, directs, and assesses air and space operations over North America, a vital mission that cannot be interrupted. But over the next few months, Tyndall is renovating all the utilities across the base, which will require shutting down the roads leading to the 601st Air Operations Center (AOC).
“Right now we’re figuring out alternate means of access to the AOC and we’ll come up with one, get it approved and we’ll press forward,” Bartlow said. “That’s one thing that fortunately we identified well enough in advance.”
Kongaika expressed concern for his Airmen’s safety amid the congestion and construction.
“We have to have a really heightened sense of situational awareness around us, so I’m always preaching safety,” he said. “I want to empower our Airmen to knock it off or slow it down whenever they see things that are the three Ds: dumb, dangerous, or different.”
Maintainers with the 95th FGS are adapting to the circumstances. Their main depot for tools and spare parts is about a mile away and across a security checkpoint from their temporary facility, which can disrupt workflow, so they set up a smaller warehouse in a side room of their current building, reducing the number of back-and-forth trips.
Sustaining a fighter squadron requires thousands of spare parts and equipment such as rolling tool boxes, torque wrenches, screw drivers, pliers, engine covers, safety gear, latex gloves, and more. Col. George Watkins, the commander of the 325th Fighter Wing, likened it to “standing up a super-sized AutoZone.”
But a successful fighter generation squadron also requires the right culture to sustain mission-ready aircraft every day, even in difficult weather. While finding experienced F-35 maintainers is not as difficult today as it was a few years ago when the jet was brand-new, it will take time for the 95th FGS to learn how to work as a team.
“We have not worked as a team to generate aircraft; we’ve all done it individually at different places,” Flores said. “We have to make sure we have the communication in place and the expectations set so we make the right call and follow the right processes. We’ll learn but I think that’s just part of the growing process for a new team.”
Kongaika pointed to the arrival of the first F-35s as crucial to building that teamwork.
“There’s nothing that replaces hands-on training, so we need some aircraft in order to train,” he said.
Barring further production delays, the 95th Fighter Squadron should reach full operational capability with 24 primary assigned aircraft and two more in reserve by the middle of 2025. The number of 95th FGS maintainers will also grow from about 50 people on the ground today to an end-strength of 200. Becoming operational will take sweat and coordination, but the new aircraft, the new hangars, and the chance to build a new unit from the ground up has its rewards too.
“Seeing our own aircraft in front of the squadron with the Tyndall tail flash on it … it’s just a good feeling, and I think that’s what everyone is excited about,” said Flores.