Blacksmiths have produced weapons and armor for thousands of years, and the Air Force still relies on them today to shape metal into aircraft parts. But emerging technology could introduce a new form of blacksmithing where artificial intelligence makes the fine-tuned decisions involved in bending metal into specific shapes that can help military aircraft stay ready for action.
A robot prototype, nicknamed AI-FORGE, arrived at the Warner Robins Air Logistics Complex (WR-ALC) at Robins Air Force Base, Ga., in late January and successfully conducted its first field test, according to a recent Air Force press release.
Developed at The Ohio State University in partnership with the Air Force Research Laboratory, the Advanced Robotics for Manufacturing (ARM) Institute, CapSen Robotics, and Yaskawa Motoman, AI-FORGE was tasked with forging relatively simple parts for six hours in conditions like those seen at WR-ALC and other depots.
“We picked a relatively simple part as the demonstration unit because, first, we had to see if it is even possible to do this type of work in a depot environment, and we determined that it absolutely is,” Shane Groves, the lead automation engineer at WR-ALC, said in the Air Force press release. “That’s why I think this was one of the most successful ARM demonstrations we have ever seen here at WR-ALC because we established that yes, the system was able to operate autonomously and complete the task in a very taxing environment.”
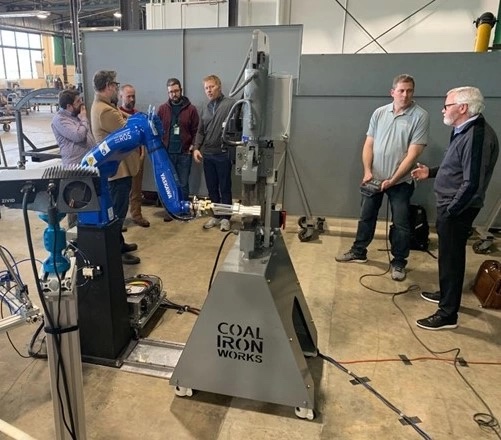
Moving forward, Air Force officials and experts say the sky may be the limit for what the system could manufacture.
“In the near future, this system will allow us to acquire the specific auxiliary components and tools that are required to successfully support DAF missions,” Dr. Sean Donegan, digital manufacturing research team lead for AFRL’s Materials and Manufacturing Directorate, said in a statement. “But in the far term, we want to be able to make almost anything.”
For the Air Force, that could mean reproducing even the most complicated aircraft parts.
“We want to make shapes but also control how we get there, in order to produce repeatable results,” Dr. Michael Groeber, associate professor of the Integrated Systems Engineering and Mechanical and Aerospace Engineering departments at Ohio State, said. “Then we can start to get into some really clever designs that will ensure performance [in aircraft or other systems].”
Having a robot capable of producing complex aircraft parts could be crucial for the Air Force, which frequently struggles to find replacement parts for its aging airframes, the production lines for some of which have been closed for years. In fact, maintainers often have to cannibalize replacement parts from other aircraft to cut down on the wait time to get those platforms back up and running.
Combat metals Airmen have a reputation for manufacturing such parts both at home and in deployed environments, but with a labor shortage in trade skills such as metal fabrication, robot blacksmiths may be able to help close the gap. Groves told Bloomberg in February that parts made with robot blacksmiths from the company Machina are shaped better, stronger, and faster than those made by humans.
“The main problem we have right now is that companies have plenty of work, and when I ask them for one or two parts, they don’t see the return in tooling everything up for a small order,” he told Bloomberg. “We’re getting quotes for four-year delivery times to get some of the right parts.”
Getting the AI to the point where it can match the work of Airmen is no small feat, though.
“When a human blacksmith forges a piece of metal into a specific shape, they have to make all kinds of decisions on the fly,” Donegan said in a release.
Some of those decisions include how to orient the component, where to apply force, how much heat to use, and when to put it back into the furnace.
“A skilled artisan blacksmith can make decisions like these without even thinking about them, and our research team is especially interested in how to replicate that kind of decision-making process [with artificial intelligence],” he explained.