The average age for America’s fleet of F-15C Eagles is about 38 years old, and many of the aircraft’s spare parts are no longer produced or can take days to order from a manufacturer. Luckily, the Oregon Air National Guard’s 142nd Wing has a metals technology shop at Portland Air National Guard Base where Airmen fabricate parts in-house to keep the wing’s elder Eagles flying.
“We have the ability as a unit to say, ‘Hey, stop what you are doing. We need to have this part made,’ and then have that part made in hours or even minutes,” Staff Sgt. Nathan Carssow, an aircraft metals technology craftsman with the 142nd Maintenance Squadron, said in a Nov. 29 news release about the shop.
Some of the parts help hold the plane together. Recently, the craftsmen made an aluminum stringer for the F-15C’s tail cone. The stringer is one of three stiffeners that provide a framework for the tail cone assembly that airframe skins and smaller parts attach to, Master Sgt. Steph Sawyer, a spokesperson for the 142nd Wing, told Air & Space Forces Magazine.
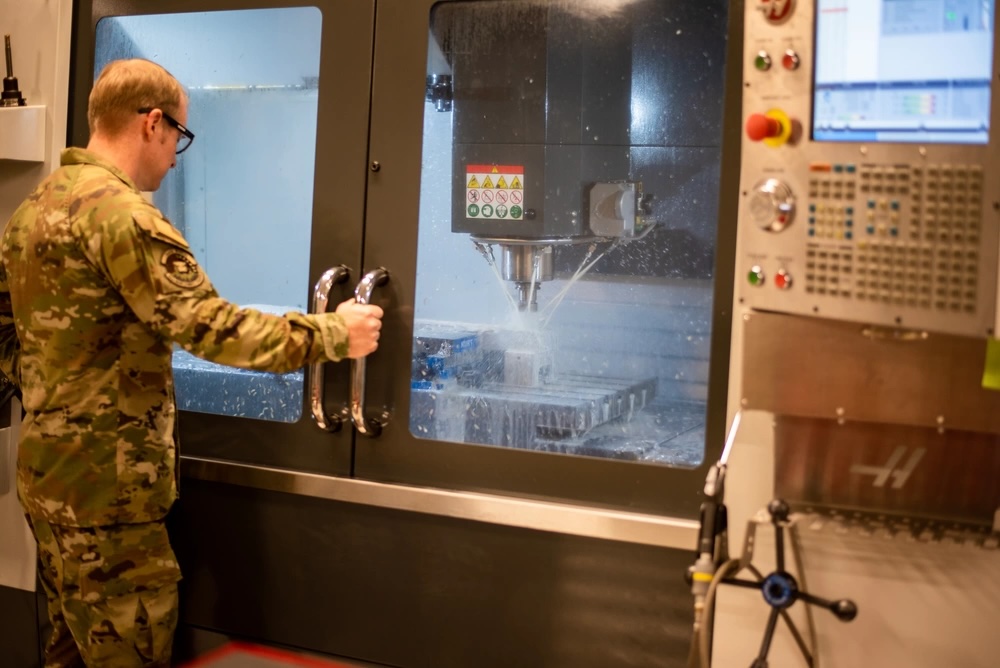
Another type of key part are bushings, which often look like small thin tubes that reinforce functional holes in the aircraft which have weakened with wear.
“In the more intricate parts of our job, if an aircraft is in need of something, like the bushings, it’s not going to fly until our shop finishes the project,” Tech. Sgt. Nate Brown, a 142nd Maintenance Squadron metals technology craftsman, said in the release. “ … When a job is serious enough to need metals tech, it’s not going to fly until we finish the project that’s been given to us.”
Turning metal into a part ready for the demands of military aviation requires special tools, including manual lathes, CNC (Computer Numerical Control) mills, 3D printers, and welding tools. Other tasks are less demanding but just as important, like removing screws stuck in removable panels or skins.
“Stuck screws can cause a work stoppage due to the maintainers being unable to access those areas to accomplish maintenance or inspections,” Sawyer said.
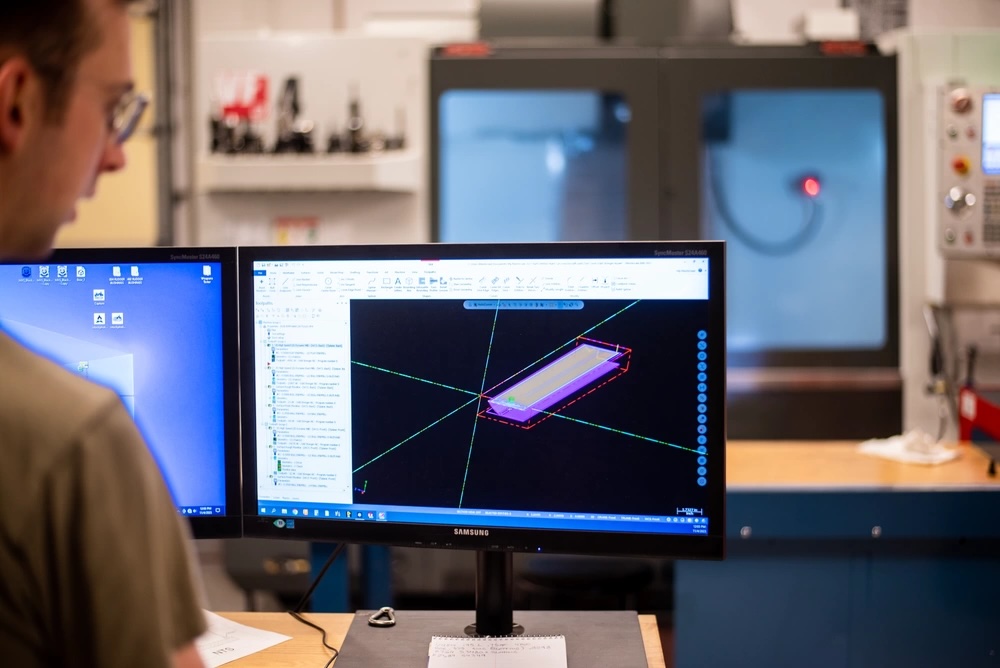
Despite fewer than 10 Airmen working there, the shop has made quite a dent, saving $1.2 million in Air Force Repair Enhancement Program (AFREP) funds in fiscal year 2023 alone. When Airmen fix a part through AFREP, the unit can take the money that would have gone towards a replacement part and instead use it on capital improvements or new equipment. The same goes for non-aircraft parts, such as those used by aerospace ground equipment, ammunition, or other shops that keep the service running.
Metal shops can be especially helpful for older aircraft like the F-15 or the RC/WC-135, but even younger jets sometimes need creative in-house fabrication. For example, the Air Force’s fleet of F-35 fighters is just four years old on average, but AFREP Airmen at Hill Air Force Base, Utah saved the base thousands of dollars by designing better F-35 sensor covers and better diagnostic tools for the stealth jet.
That means when the Oregon Air National Guard starts flying brand-new F-15EX Eagle IIs in fiscal year 2025, the Airmen at the metals shop will probably still have plenty opportunities to test their mettle.