When left unchecked, the corrosion of metals and alloys is inevitable and extraordinarily costly. U.S. companies spend an estimated $276 billion annually on corrosion prevention, mitigation and repair – more than 3% of gross domestic product (GDP).[1] And for the U.S. government, unmanaged corrosion can pose serious problems across its assets and infrastructure, impacting mission readiness, crew safety and systems reliability. That’s why the U.S. Department of Defense (DoD) spends around $20 billion annually on corrosion maintenance – almost 20% of every dollar budgeted for maintenance purposes.[2]
Battelle has helped the DoD with many of its corrosion challenges. The independent nonprofit science and technology research organization has multidisciplinary and comprehensive materials science and engineering expertise that uniquely position it to solve the most challenging material problems. And with its well-equipped facilities and multidisciplinary resources, Battelle can perform systematic material characterization assessments like material development, performance, qualification and specific failure analysis. When Battelle’s full material capabilities are brought to the table, myriad challenges – from unique materials selection to specific corrosion issues – can be solved to minimize maintenance costs and ensure critical systems are always mission ready in support of the warfighter.
Fighting Corrosion Requires Tailored Solutions
The U.S. DoD agencies deploy a wide array of equipment and assets that execute wide variety of missions under various states of duress in a plethora of environments. As such, the exposure profiles and corrosion impacts on these assets in deployment are diverse and unique to their mission. There is no one-size-fits-all solution to military corrosion challenges. For example, the operating environments for a Naval Ship, a Coast Guard Cutter, a Marine Corp Mine-Resistant Ambush Protected (MRAP) or an Air Force fuselage vary significantly, depending on location, specific usage, the materials involved, the age of the equipment and much more.
Battelle has multiple indoor and outdoor facilities for research and development, characterization and the testing and evaluation of advanced materials. At its Center for the Characterization of Advanced Materials (CCAM), Battelle has laboratories explicitly designed for coatings research and development, as well as advanced characterization systems for spectroscopy, microscopy, failure prediction and analysis. The Center also houses equipment for weathering and cyclic exposures, which enables Battelle researchers and scientists to evaluate the impact of various environmental conditions on specific materials.
At its one-of-a-kind Florida Materials Research Facility (FMRF), Battelle can conduct outdoor materials characterization to assess atmospheric and marine exposure of materials. (See Figure 1.) It’s located in one of the most corrosive environments on Earth and the property includes the only commercial oceanfront facility for subtropical exposure studies in the U.S.[3] It’s also equipped with a wide array of exposure racks and fences that conform to American Society for Testing (ASTM) materials and two acres of beachfront exposure area that’s less than 70 meters from the Atlantic Ocean. This means Battelle can expose sample materials to nature’s harshest elements – like sun, wind, seawater spray and more – at any angle. Located on the Intracoastal Waterway via the Halifax River, FMRF also boasts access to tropical and subtropical marine fouling organisms with a level of biodiversity that is not achieved further north or south. This enables Battelle to test marine materials, antifouling coatings and foul release products in fully submerged, floating waterline and splash zone exposures on its marine immersion dock in the harshest of fouling conditions available. With the ability to perform both ASTM and Military Spec testing, Battelle can support failure analysis, material evaluation and qualification against the most rigorous standards.
In addition to testing, Battelle excels at studies on material compatibility and analysis of alternatives (AoAs). With its extensive capabilities and background in failure analysis, Battelle can identify key material properties and conduct AoAs to achieve system requirements. For example, Battelle has assessed coating vulnerability for specific applications and environments and proposed formulation enhancements to ensure the coating’s integrity and its ability to protect the substrate.
Additionally, Battelle has a team of subject matter experts evaluating impacts of biological growth (such as fungi, bacteria etc.) on coatings used on a variety of substrates within the DoD. As part of a recent project for the U.S. Air Force, Battelle worked with a coatings manufacturer to improve the weathering performance and resistance to microbially influenced corrosion of a powder coating used on aircraft ground support equipment in Pacific locations with hot and humid operating conditions. Battelle also recently evaluated an in-field corrosion repair technique used by the U.S. Naval Air Systems Command (NAVAIR), assessing the application of inorganic coatings to prevent galvanic corrosion of dissimilar substrates. In addition, Battelle is currently evaluating nine coatings of five different U.S. Army manufacturers in support of their acquisition decision on non-developmental items.
Combating the Slow Creep of Corrosion
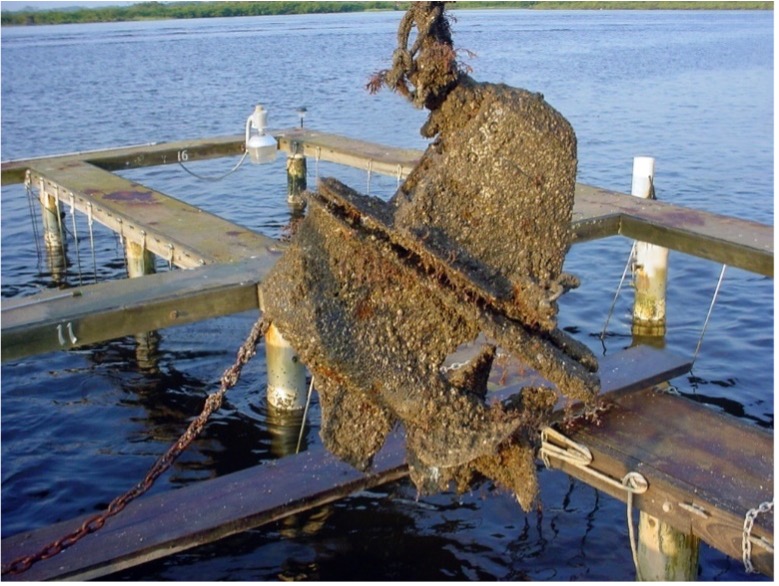
Corrosion occurs at a slow pace – by the time it is visible to the eye, the damage can be especially costly to repair. To help the U.S. government stay ahead of the curve, Battelle can perform accelerated life testing to make informed predictions about root cause material failure and its probability for occurrence. This is especially useful for mitigating risk with military vehicles and equipment during deployment – from tactical vehicles to ground support equipment. As part its Corrosion Prevention and Control (CPAC) program with the U.S. Marine Corps, Battelle has assessed new coatings and corrosion prevention compounds, reviewed repair processes, created systems to more effectively preserve equipment, and identified where future investments could be made.[4]
When it comes to fighting corrosion, proactive planning and prevention not only mitigates risks, but can also save millions of dollars. Worldwide corrosion authority NACE International estimates that proper corrosion management could save as much as $375 to $875 billion annually.[5] For the U.S. and the various branches of U.S. military, Battelle’s unmatched expertise and ability to conduct total life cycle management is particularly germane and beneficial. With these capabilities, it’s possible to extend the service life of vital government and military assets, which reduces overall ownership costs while improving mission readiness – a true win-win scenario.
Visit Battelle.org to learn more about the company’s advanced materials expertise.