Halfway through its two-year charter to quickly inject new technologies into Air Force maintenance, support, and repair, the Air Force’s Rapid Sustainment Office is doing what its creator, USAF acquisition chief William Roper, had hoped.
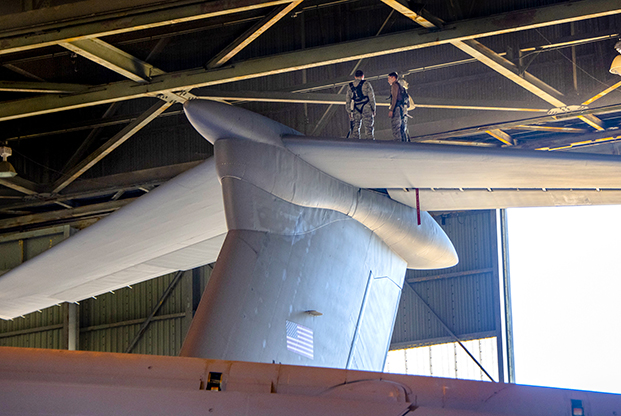
“Nothing is as fast as I would like,” Roper said at the Air Force Association’s 2019 Air, Space & Cyber Conference in September. “But I’m actually really impressed how quickly the technologies are moving, now that results have been demonstrated.”
In the year since its launch, the RSO experimented with condition-based maintenance, additive manufacturing, cold spray technology, robotics, automation, and virtual reality. It’s also entered a public-private partnership with Delta Air Lines to gain insight into that company’s successful predictive maintenance systems.
Lt. Gen. Robert D. McMurry Jr., program executive officer for the RSO and commander of the Air Force Life Cycle Management Center, said the RSO doesn’t quote savings targets. But he told Air Force Magazine in an interview that “we’re trying to show an impact on the order of half-a-billion dollars in a couple of years.”
Based on existing projects in condition-based maintenance, “agile manufacturing,” and automation, the RSO said it can claim $68 million in costs saved or avoided so far, “with a return on investment of 66 percent over the life cycle.”
Roper conceived of the RSO idea in 2018 after noticing that the Air Force invests most heavily in weapon systems during design and development, and far less in maintainability. Given that 70 percent of the cost of a weapon system is expended to sustain its operation, he saw untapped potential for savings if sustainment costs could be reduced. He modeled the new RSO after the Air Force’s Rapid Capabilities Office and the Pentagon’s Strategic Capabilities Office, which Roper headed before coming to the Air Force job.
Like those organizations, the RSO is meant to identify promising technologies, experiment with their use, and aim for big payoffs by reducing costs, saving time, or improving system availability.
RSO Deputy PEO Nathan Parker said the office has about 24 people today, and that will continue to grow as new project areas come online. “But it’s purposely meant to be a small team that has a focused mission to solve their problem and then move on,” he said. “It’s not meant to be a 500-person organization. It will never grow to that.”
Among the most visible successes so far: “Condition-Based Maintenance Plus,” which tracks aircraft individually, by tail number, and as a fleet—seeing how the aircraft is used, when parts typically fail, and when service on subsystems really are needed.
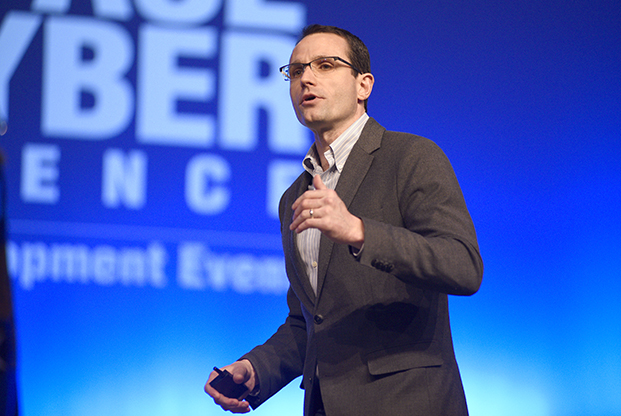
Roper cited “40 algorithms that immediately started saving money” in C-5M Super Galaxy maintenance, explaining that the approach has been especially effective in “reducing the amount of time that planes are down due to part failure.” Breakdowns can strand a plane and crew for days while waiting for parts to arrive if none are available locally.
In one case, sensor data indicated false alarms were causing maintenance crews to unnecessarily replace doors on a C-5M refrigeration system. Instead of spending $250,000 to replace the doors, they were able to replace the faulty sensors at a cost of just $1,400. Similarly, data derived from an existing sensor in the B-1 tail is now being used to predict “when fuel bladders are likely to lose balance,” akin to “an oil change light coming on in a car.” That means crews can take action in advance.
In other words, Roper said, the “algorithmic oracle that can see the future is not just money in the bank, it’s readiness to the warfighter.”
The commanding general at Air Mobility Command, Gen. Maryanne Miller, is so enamored with Condition-Based Maintenance Plus that she wears an “I Love CBM+” T-shirt every Friday, Roper said, adding that AMC is pressing to expand its use across the mobility fleet: “So they can manage it like an airline.”
The KC-135 also uses CBM-plus, McMurry said, and nine other platforms are using similar analyses.
Now the fighter community is getting on board, starting with F-16s, Roper said.
Impressed by Delta maintenance programs, McMurry said, the Air Force is modeling its programs on the airline’s success. “They went from 255 maintenance cancellation days in a year to 300 straight days with no maintenance cancellation,” he said.
Delta, and its partner Georgia Tech, have been enthusiastic supporters. “They have embraced us, they’ve shown us how they manage their fleet, made their tools and algorithms available to us, and given us great feedback on how we get to good—which is where we are now—and then the increasingly difficult challenge of getting from good to great,” Roper said. McMurry also said the Delta/Georgia Tech team is working with Wichita State University in Kansas and Airbus to develop additional predictive algorithms.
Not every RSO effort will yield clear cash savings, McMurry noted, but that doesn’t mean there isn’t a return on investment. “The question is, how do you value a return to operations” he asks. “If you save three weeks of downtime, how do you value that? Whereas if I manufacture a part for $4,000 that usually costs $160,000, OK, I’ve got a pretty good understanding of what that savings is.”
Nevertheless, Parker said, the RSO was structured to pay for itself. “So every project we spend money on, we look at it through the lens of, does it save dollars? Does this technology, in addition to increasing readiness, have the potential to drive down costs”
That’s how Roper wanted it, McMurry said, “that the Rapid Sustainment Office should develop projects that will pay their own way.” And it is.
Roper said other RSO initiatives include additive manufacturing, also known as 3-D printing—“which is just a no-brainer,” he said—and using robotic lasers to remove paint.

3-D PRINTING
Additive manufacturing provides an affordable means to generate parts that have been out of production for decades. The parts can be measured by lasers, potentially improved, and then “printed” using machines that lay down multiple layers of material until the part is formed. Parts can be created without having to hold a supplier competition, go through design, development, testing, and certification, and don’t require minimum orders of dozens or hundreds when only one or two are needed.
When C-17s needed new ventilation ducts, McMurray said, additive manufacturing was the answer. “We don’t have to wait on these parts, which really weren’t designed to be fixed very often,” he added. For now, additive techniques are limited to non-flight-critical parts, but a spokesman said experiments to print flight-critical parts—those subject to extensive dynamic stresses—are about three years away.
AFLCMC has approved 153 critical additive parts so far, either metal and polymer, for C-130 and C-5M transports, and has developed a “part tracking tool” to monitor how they perform and how much they cost or save in the long run, the RSO said.
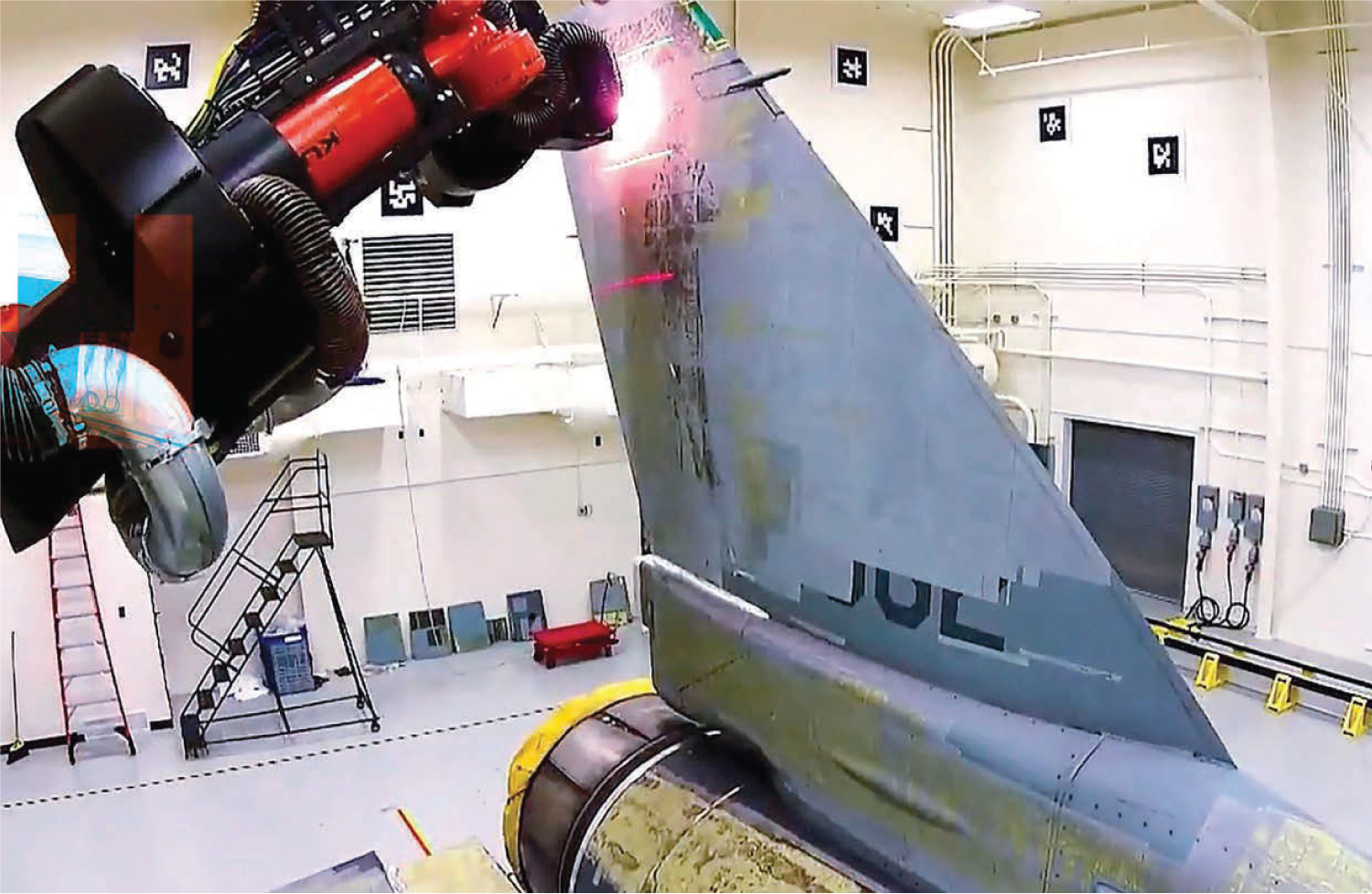
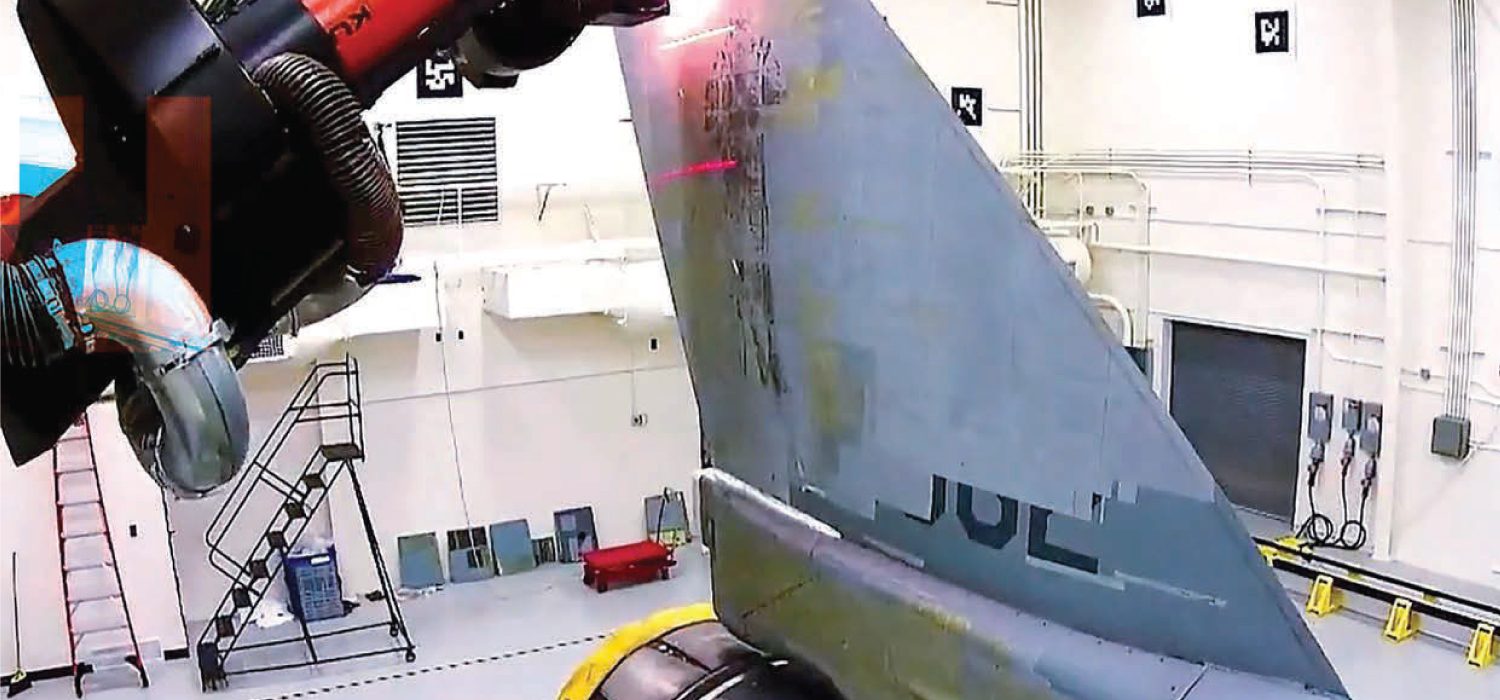
LASER PAINT REMOVAL
The laser paint removal system installed at Hill AFB, Utah, uses a laser mounted on a robotic arm to remove paint to specified depths in days rather than weeks. Previously done with blast beads, the process of depainting an F-16 used to produce about a ton of hazardous material, and required workers to wear elaborate safety gear to protect them from toxic hexavalent chromium. The laser system essentially burns away most of the hazardous waste and sucks up what isn’t burned with a vacuum, leaving only about four ounces of hazardous waste. Operators of the machine sit in a room nearby and don’t have to don any protective garments or respirators.
“The challenge there,” McMurry said, “is that to put more of those bays in requires more capital investment. And probably [military construction funds] as well.” Roper said the technique will be expanded to every depot and the Aerospace Maintenance and Regeneration Group, which operates the “boneyard” at Davis-Monthan AFB, Ariz.

using a carrier gas to accelerate the metal particles through a supersonic nozzle. Source: Ellsworth AFB, S.D., video
COLD SPRAY
Cold spray is another new technique. The process involves the precise, computer-controlled deposit of metal onto a worn area of an existing part. New metal is sprayed on and the speed and temperature of the process ensure it bonds permanently to the underlying metal. Parts can then be machined and made as good as new.
Instead of replacing an entire gearbox, McMurry said, only the worn parts need be repaired. On an F-16, a new gearbox might cost $180,000. But “with cold spray you can actually repair that for about $4,000,” McMurray stated. “So, it’s a pretty big deal.”
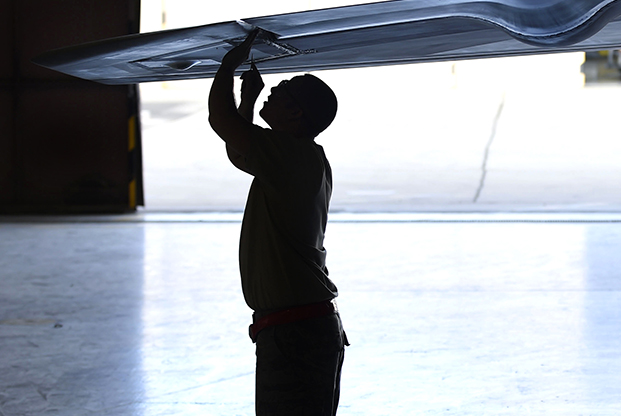
SPREADING THE WORD
After proving its initiatives can pay for themselves, Roper said, the next step is to see if the Air Force can “scale them across a fleet and then across a mission.” The biggest limiting factor, he said: “A lot of our logistics data is on paper.”
Roper is eager to move logistics data to a digital cloud where analytics and machine learning can be applied to drive even greater savings. “It is just so compelling to think about what data analytics might do, [and how they might] give us insights we might not otherwise have on the fleet,” he said.
The RSO goals are to develop an “ability to”:
- Counteract obsolescence in aircraft, support, and test equipment.
- Accelerate training using virtual and augmented reality.
- Capitalize on analytical decision tools and untapped data.
- Better understand and predict aircraft, munitions, and equipment condition during operation and prior to induction into major inspection and maintenance.
- Rapidly accomplish low-observable maintenance, in order to improve aircraft availability and mission capability.
- Deploy rapidly constructed maintenance structures to support operations in austere locations. This is part of the Air Force strategy for keeping peer adversaries guessing about where USAF assets might be in time of crisis. Structures providing a dry, cool environment are critical for repairing low-observable coatings, which take longer to cure in hot climates.
- Support a common operating picture across multiple battle spaces for enterprise logistics sustainment.
Depots are a big factor in sustainment operations, and McMurry said the focus there will be a “renewed emphasis on material availability to support the work we do.” There will also be a push to “get their workforce fully staffed with certified and capable technicians” and help them “compete for talent on the human resources side, in order for them to be effective and competitive.”
Depot is “always a big factor” in whether aircraft are available or not. But it’s important to remember, he said, that “they’re often there because we’re modifying them to put in new capability,” and usually it’s the depot that has the “material and technicians to do that work well.” The RSO will also be looking at “how do you optimize the depot workload across the three centers”
After the two-year trial of the RSO comes to an end in October 2020, what happens then
“We will make a recommendation back to the Secretary [of the Air Force] on the permanence of the organization next year, based on the guidelines and the charter—whether we’re able to meet the mandate,” Parker said.
While “we haven’t been extended, … we haven’t asked to be extended either,” he said. “We’re basically executing the intent of the charter right now, and as we get into next year we’ll make that assessment and recommendation. But all indications right now are very positive.”